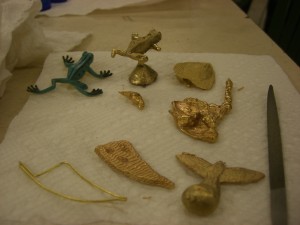
Starting from the frog and going clockwise: Delft clay casting, cuttlebone leaf, water casting, cuttlebone bird and tooth shape.
I took a class this weekend at Artisan’s Asylum called Metalcasting with Sand, Bone, and Water. We learned how to cast shapes freeform, by pouring molten metal into water, how to carve shapes in cuttlebone (which gives you great ripply textures from the cuttlebone – one more tutorial for good measure), and how to use Delft clay (really sand mixed with some kind of oil) to make a mold of another object, and then recreate it with metal.
It was really terrific fun, one of my favorite classes I’ve taken there, and I highly recommend it (I believe it will be run again at some undetermined point).
I attempted to cast my little toy frog using the Delft clay, but its legs are so thin that the metal really couldn’t make it down their full length, so the results are what you see above: a frog with sad little stumps. (Though with a little of the burnt sand/oil mix still on the surface, it could almost pass as some ancient artifact that has mostly survived some great catastrophe. Froggy de Milo?) This is a great method for recreating something that has a lot of fine detail – one person used little plastic fish (flexible, though not as badly as the frog, so it took some extra care to make sure it left a good impression in the clay) – and the results are amazing. It picked up every scale and fine line in the fish’s fins.
We did the water casting to gain some familiarity with the process of melting the metal and then pouring it. The target is a bowl of water, as opposed to the small funnel that we cut into the clay or cuttlebone to pour metal into. (You can see part of the funnel there on the frog’s base.)
The shape is impossible to control precisely, but the height of the crucible above the water does determine how much the metal spreads out. One of the other students got a really interesting shape, like a wide, flat, curving ribbon, by “throwing” the metal into the water. This would be a fun technique to play around with more. (Other people suggested trying things spinning the bowl of water; dropping the metal into a much deeper bowl so that the bottom of the metal would be round instead of flattening out; and dropping the metal into boiling water to see what the bubbling would do.)
The cuttlebone turned out to be my favorite method. The texture that the pieces end up with is so fantastic – it is great for narrow wiggly organic shapes, and for things like wings and fish.
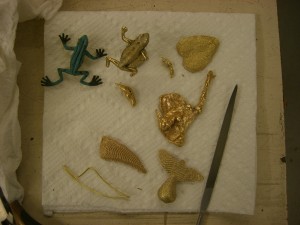
The other side of some of the shapes.
For two of the cuttlebone castings, I attempted to shape both sides. The mold is made by sanding two cuttlebones flat, carving your design into one surface, and then taping them together to pour. It is difficult to figure out how the outline of your shape would show up on both halves of the mold, so usually the cuttlebone shapes are flat on their back side (well, flat except for the natural grain of the cuttlebone).
For the leaf and tooth shape, I attempted to give both sides some depth. With the leaf, I just kind of guessed, and carved the reverse side significantly smaller than the front.
For the tooth, I bent a piece of brass wire into my outline, and then sandwiched it between the pieces of cuttlebone, pushing them together to press the wire into the bone, before beginning to carve – the wire left a nice outline on both pieces for me to follow, and I did get some depth on both sides of the cast. I ended up liking the “reverse” side of the tooth better, because I cut it deeper and with a little more curve to it, and the deeper, more curved shapes showed the texture of the cuttlebone better.
For the last piece, I wanted to really take advantage of the texture, have it work well with the overall form, so I carved a really abstract bird, with spread wings, into the cuttlebone, hoping the ridges would look like really abstracted feathers.
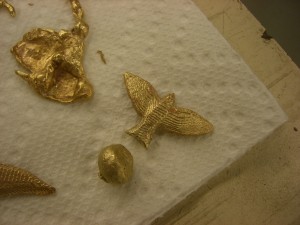
Bird cast in cuttlebone, with the sprue cut away
I didn’t do any major finishing for the pieces – I trimmed the sprues and filed the sharpest edges down, but I haven’t taken any polishing wheels to them, so they look a little dull (really. after going through several steps of polishing, that brassy metal GLEAMS).
I think it would be really neat to cast some bezels or frames in cuttlebone that I can wire stones into. I think the ridged texture could look really fantastic. The metal we were using for most of the work was some sort of copper alloy (it looks very similar to brass, but I don’t know if it was alloyed with tin or zinc or what), and quite soft, so I could also cast narrow shapes and wind them around stones, like a really, really fat wire. A couple of students brought in silver jewelry they no longer wore, and melted that down for casting; there was additional sterling casting grain on hand that we could buy if we wanted to, but since I was more focused on experimenting with carving shapes into cuttlebone, I didn’t feel like splurging.
There are plans in place to set up an area at the Asylum that is dedicated to jewelry work (and glass – lampworking!!!), which I am really looking forward to.
Of course, I’m going to want to cast steel, too.